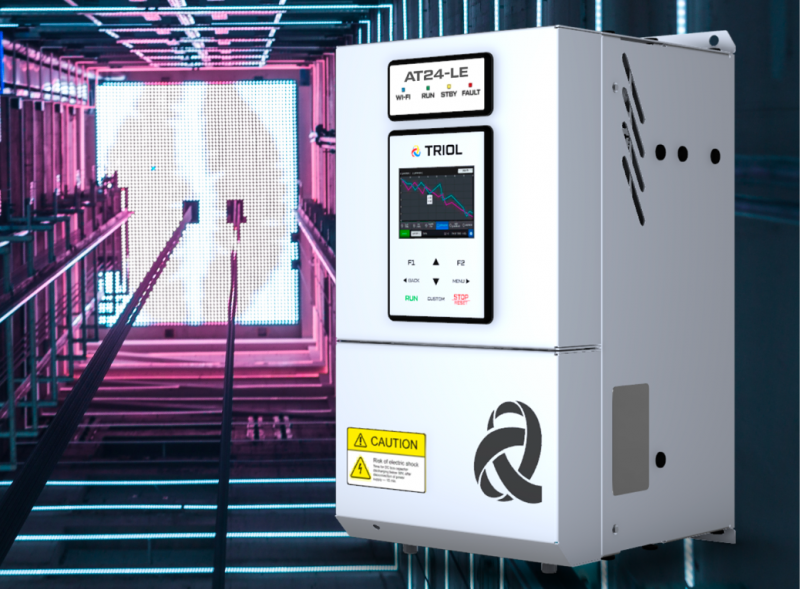
VFDs for elevator applications
Elevators are a very demanding and a demanding application for VFDs.
Elevator application puts forward special requirements for frequency drives:
- high accuracy of speed regulation, regardless of the load of the elevator car;
- constant acceleration and deceleration combined with the creation of comfort for the movement of passengers;
- high overload capacity and ensuring high dynamics of movement;
- a guarantee of passenger safety and operational reliability.
The challenges we set ourselves to satisfy each of our customers and users and our solutions.
Continuous monitoring of the continuity of the circuit from VFD to the motor is carried out by monitoring the currents according to a special algorithm - in case of an incorrect current change per unit of time, the AT24 LE drive generates an alarm message with the output voltage disconnected and the brake applied. This function promptly notifies of a motor failure or its power supply circuit and prevents the use of faulty equipment.
Broken braking resistor monitoring - The VFD checks the presence of a braking resistor before each drive, which minimizes the possibility of using faulty equipment. Failure of the braking resistor can lead to an emergency stop of the VFD and the elevator car itself.
The "evacuation of passengers" mode when the standard power supply of the elevator is turned off and switching to power supply from the UPS (uninterruptible power supply ~ 1 phase 220 V) ensures the leveling of the car according to the level of the nearest floor with the possibility of moving towards the least resistance. This allows passengers to leave the elevator until it comes to a complete stop, rather than staying in the elevator car between floors until the arrival of the service.
Ability to deeply configure start and stop parameters.
Acceleration and deceleration is carried out with control not only of the acceleration and deceleration times, but also of their derivatives: acceleration and jerk, which are regulated by the parameters of VFD. This makes it possible to achieve the most comfortable start of the elevator car (the moment of car lift-off is not felt).
Example of an acceleration curve without acceleration limitation
Acceleration curve example without acceleration and flick limitation:
Where:
blue - speed,
red - acceleration (first derivative of speed),
yellow - jerk (second derivative of speed).
Example of an acceleration curve with acceleration and flick limitation:
Where:
blue - speed,
red - acceleration (first derivative of speed),
yellow - jerk (second derivative of speed).
The high PWM frequency of 8 kHz of the VFD AT24 LE guarantees a low noise level from the electric motor during the movement of the elevator. The lack of a "squeak" of the semiconductor devices of the VFD and the noise from the operation of the winch do not cause complaints from the residents of the upper floors of the building
The adaptive algorithm for measuring the motor speed using an encoder allows the speed to be calculated with high resolution at low engine speeds at frequencies from 0.01 Hz to 0.5 Hz. The start and stop of the elevator becomes even smoother and more comfortable, and the stopping accuracy of the elevator car does not exceed +/- 10 mm
A full cycle of VFD testing in extreme modes of temperature and at declared overload capacities in combination with the use of semiconductor devices of world brands (Infineon, Semikron) and film capacitors (with a service life of at least 100,000 hours) guarantee long-term operation and a minimum number of shutdowns.
More than 25 years of experience in the development and production of VFDs.
More than 150 people in development departments.
Hundreds of thousands of commissioned VFDs.
All experience of development and implementation is applied in the new generation of AT24 LE VFDs.
Optimized cooling and heat dissipation system ensures a small footprint. This allows the AT24 LE to be used instead of any other manufacturer's VFD and even to reduce the dimensions of the elevator control station.
Cooling fan with automatic speed control depending on the VFD temperature, optimizes losses and reduces noise.
VFDs AT24 LE are designed for use in elevators with a lifting capacity of 400 - 1000 kg.
Power range is from 4 kW to 30 kW for voltage ~ 3 phases 380 ... 480 V.
Overload capacity 150% for 60s, 200% for 3s.
Working with asynchronous and synchronous winches, with and without a gearbox.
Support for various types of encoders - incremental, EnDat, sin / cos.
Control types: vector control in open-loop and closed-loop system, scalar (U / f characteristic).
Measurement of motor parameters without rotation.
Built-in brake wrench.
Emergency braking with safe torque off STO (Safe torque off).
Work at zero speed.
DC braking.
Mechanical brake and motor contactor control.
AT24 LE VFDs allow you to work with asynchronous and synchronous winches, with and without a gearbox in the basic version. There is no need to keep several types of VFDs in the warehouse for different types of winches.
A single version of the VFD for voltage levels from 380 to 480 V.
Support for various types of encoders is available through plug-in expansion units.
Possibility of using AT24 frequency VFDs of UC and UH lines in elevator control stations. It is only necessary to add the necessary expansion units for integration into the control station.
High EMC compatibility with electrical appliances, proven by:
- CE certificate for compliance with EMC standards EN 62477-1: 2012 / A11: 2014, EN 61000-6-2: 2005 / AC: 2005, EN 61000-6-4: 2007 / A1: 2011;
- Certificate of conformity IEC / EN 61800-3 for application categories C2;
- Certificate of conformity EN 61558-1: 2015.
The wide range of programmable signals and control functions of the AT24 LE ensures its integration into any control station.
The ability to install simultaneously up to 4 expansion units: discrete and analog inputs / outputs, support for different types of encoders, interface units (Modbus TCP, CANopen, Profibus).
The presence of macros in the software with the configuration of discrete inputs and outputs for the elevator control stations. Possibility of creating new macros for other control stations.
Full configuration and start-up of the control station using a macro is carried out in no more than 26 steps in 5-10 minutes.
Saving the parameter settings in the remote control software (basic Wi-Fi remote control, optional operator consoles) with further application of these settings to other AT24 drives. Fast and convenient!