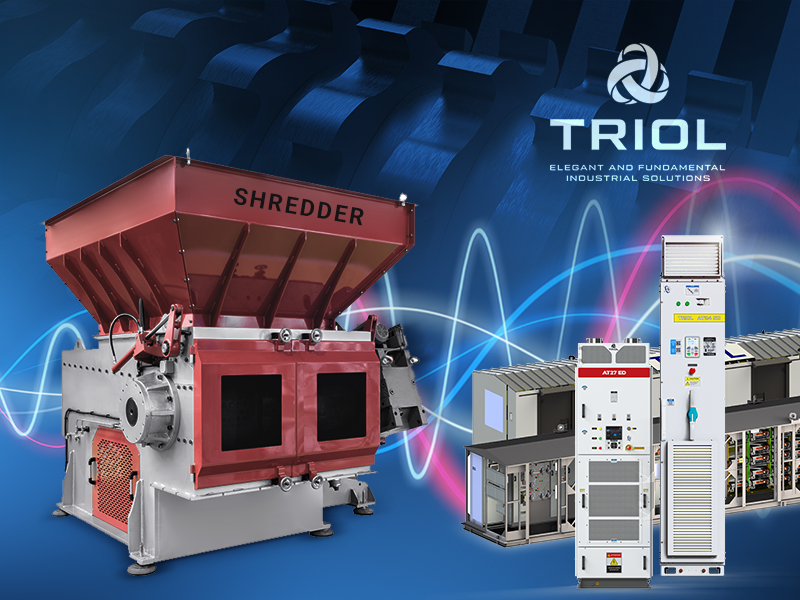
Shredding is an essential step in the processing of solid industrial and municipal waste (recyclable waste). There are several levels of shredding depending on the recyclable materials. Shredders are involved in the recycling process.
Though they are intended for the same purpose, shredders are different by design and are divided into grinders:
- with one shaft;
- with two shafts; and
- with four shafts.
The main applications for shredders are:
Bulky waste, including old cars;
- scrap metal;
- household waste;
- industrial hazardous waste;
- waste tires;
- plastic; and
- cardboard.
Triol Corporation sees the following technological and economic challenges facing the shredder owner
- Equipment lifetime extension
Straight motors start and no torque limitation leads to accelerated motor and mechanism degradation, which leads to additional repair costs and increased costs of recyclable materials processing.
- Non-stop process
The appearance of abnormal equipment shutdowns related to the quality of the supply network and delayed recyclables supply lead to an increase in processing costs, which reduces the competitiveness in the market.
- Operation in weak power mains
Unacceptable mains voltage sags and emergency shutdowns caused by non-standardized mains parameters can lead to penalties for exceeding peak power consumption and can result in additional financial losses.
- Energy consumption optimization
High competition in the recycling market requires the maximum reduction of costs for the technological process. One of the major items forming the recycling price is the electricity consumed by the equipment. Its consumption reduction leads to a decrease in the cost of processing.
- Reducing the recycling cost
The recycling market requires constant cost minimization to maintain competitiveness. Non-optimal technological process, forced downtime and large (peak) power consumption greatly influence the cost of processing industrial and domestic wastes and their optimization, which is the enterprise's priority task.
- Work in conditions of high air humidity and conductive dust
The creation of dust is possible during waste recycling of conductive materials, which means that equipment with IP20, IP31, IP41 enclosures is unsuitable for use. It is necessary to use protected equipment that allows one to work in harsh environments.
- Installation in a limited space
Recycling facilities are not always able to allocate enough space to install new equipment, and the new building construction for a frequency drive can cost around $50,000, which is not acceptable to the end-user. Therefore, the preferred option for the end-user is equipment with a minimal footprint that can be installed in an existing facility.
- Adapting to the possibilities of local ventilation and equipment maintenance
Existing production facilities include communications, particularly the ventilation system, so the preferred option for the end-user would be one that allows the newly installed frequency drive to be integrated into the existing ventilation system.
- Outdoor application
Some end-user objects have no possibility of placing the frequency drive indoors. But the construction of a new room may be economically unreasonable or fundamentally impossible. Yet the newly installed equipment must be operated in the open air with an environmental temperature from -40 ° C to +40 ° C and almost 100% humidity.